The Importance Of Process Improvement In A Company
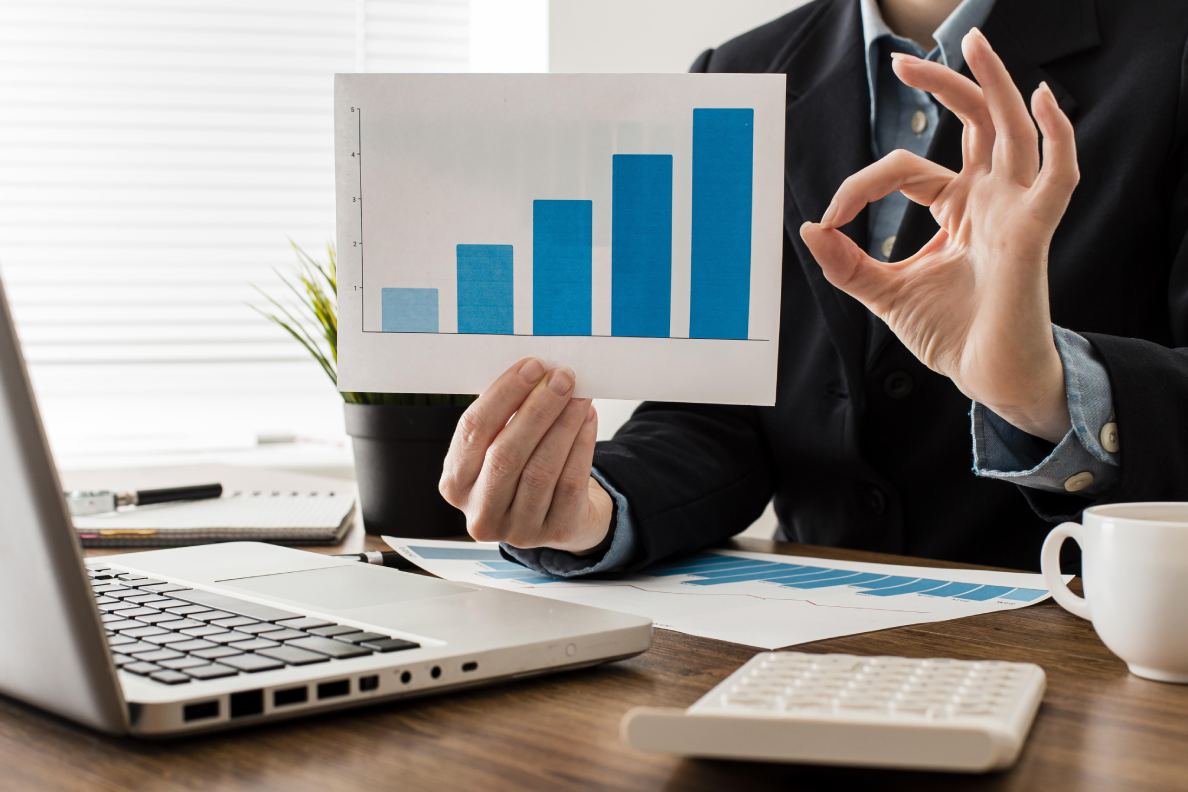
Process improvement is fundamental to the success of a company. It is a strategy that allows us to identify and solve problems in the internal procedures of an organization. Production time and costs can be reduced when processes are improved and efficiency and quality increase in the products and services offered.
Process improvement aims to optimize a company’s performance, making internal processes more efficient and effective. By improving processes, company objectives can be achieved, and this, in turn, can lead to tremendous success and profitability.
It is important to note that process improvement is not about making significant organizational changes but finding small optimization opportunities that can add significant benefits. For this, it is necessary to carry out a detailed analysis of the company’s processes to identify where the bottlenecks, recurring problems, and opportunities for improvement are.
Once the critical points have been identified, strategies can be designed to solve problems and improve processes. These strategies can include everything from procedure changes and the technology used to training staff and reviewing company policies and objectives.
Table of Contents
What Should We Analyse To Know If Our Company Is Efficient Or Not?
To know if a company is efficient, it must conduct an exhaustive analysis of various essential aspects that allow its performance to be measured and compared with market and competition standards. Here are some of the elements that need to be analysed:
- Productivity refers to the relationship between production and the resources used. Measuring the company’s productivity is essential to determine if it uses its resources efficiently and if the output is sufficient to cover the demand.
- Profitability: Refers to the ability of the company to generate profits. Profitability must be analysed to determine if the income generated is sufficient to cover costs and make a profit.
- Costs: It is necessary to analyse the company’s costs to determine if they are competitive and if resources are being used efficiently. Indirect expenses, such as overhead and human resource costs, should also be considered.
- Quality: It is essential to measure the quality of the products or services offered by the company to determine if it meets market standards and customer expectations.
- Innovation: Innovation is essential for the growth and sustainability of the company. It is necessary to analyse if the company is innovating and using new technologies and strategies to improve its processes.
- Customer satisfaction: Customer satisfaction is a priority for the company’s success. You have to collect the opinions and comments of customers to determine if they are satisfied with the products and services offered.
- Staff Performance: The company’s staff is a fundamental resource for success. A continuous review of the staff performance is necessary to determine if they are meeting their objectives and are motivated and committed to the company.
What Types Of Processes Can Be Improved With In A Company?
A company’s processes can be classified into three main categories: core processes, supporting operations, and management processes.
- Essential processes are directly related to the company’s main activity. Improving these essential processes can significantly impact the quality of the products or services offered by the company and, therefore, customer satisfaction.
- Support processes are intended to support the company’s essential functions. These processes include activities such as purchasing management, logistics, and maintenance. Improving these support processes can indirectly impact the quality of products or services by allowing essential processes to function more efficiently.
- Management processes: These are intended for the company’s management and administration. These processes include financial management, human resource management, and strategic planning. Improving these management processes can impact the company’s general efficiency by allowing more effective management of resources and better decision-making.
What Process Optimization Methodologies Exist?
Kaizen method
It is a Japanese methodology focused on the continuous improvement of business processes. It is based on the idea that minor daily enhancements can lead to significant improvements in the long run. The Kaizen method focuses on the active participation of all company employees in identifying and solving problems to improve the efficiency and effectiveness of the processes.
Ishikawa’s diagram
Also known as a fishbone diagram or cause and effect diagram, it is a tool used to identify the root causes of a specific problem. It analyzes the relationships between the variables affecting the desired result and identifies practical solutions.
Pareto chart
It is a tool to identify the most critical factors contributing to a problem. It is based on the 80/20 rule, where 80% of the issues are due to 20% of the causes. The Pareto chart helps to identify the most critical reasons that need to be addressed to fix a specific problem.
Eisenhower Matrix
It is a tool to prioritize tasks and activities based on their importance and urgency. The matrix is divided into four quadrants: important and urgent, important but not urgent, urgent but not necessary, and not important and not urgent. This matrix helps individuals focus on critical and urgent tasks and delegate or eliminate jobs that are not important or urgent.
Lean Six Sigma
It is a methodology that combines the principles of Lean Manufacturing and Six Sigma. It focuses on the elimination of waste and the reduction of variability in processes to achieve significant improvements in the efficiency and effectiveness of the company. It uses specific tools and techniques, such as continuous flow, kanban, Kaizen improvement, and data collection and analysis, to identify the root causes of problems and develop practical solutions.
These tools and methodologies are helpful for the continuous improvement of business processes and problem-solving. Each has its specific focus and can be applied effectively in different situations and business contexts. An excellent way to learn about these methodologies is In Company training.
This personalized training is adapted to the specific needs of each company, considering its structure, objectives, and particular problems. Company Trainers can work with employees to apply these tools and methodologies to their business processes, helping them identify and solve problems, improve process efficiency and effectiveness, and achieve business objectives.
In addition, In Company training can be an opportunity to encourage the active participation of employees in problem identification and solution, improve collaboration and teamwork, and increase employee commitment and motivation.
Also Read: What Does A Community Manager Do?